In the realm of transformer installations, particularly in industrial and commercial settings, ensuring a seamless process is paramount. Yet, amidst the various checks and balances, certain tests often slip through the cracks. This oversight can lead to suboptimal performance and even potential hazards. Interestingly, while attention to detail is emphasized, there are particular tests during the installation phase of transformers that are commonly overlooked.
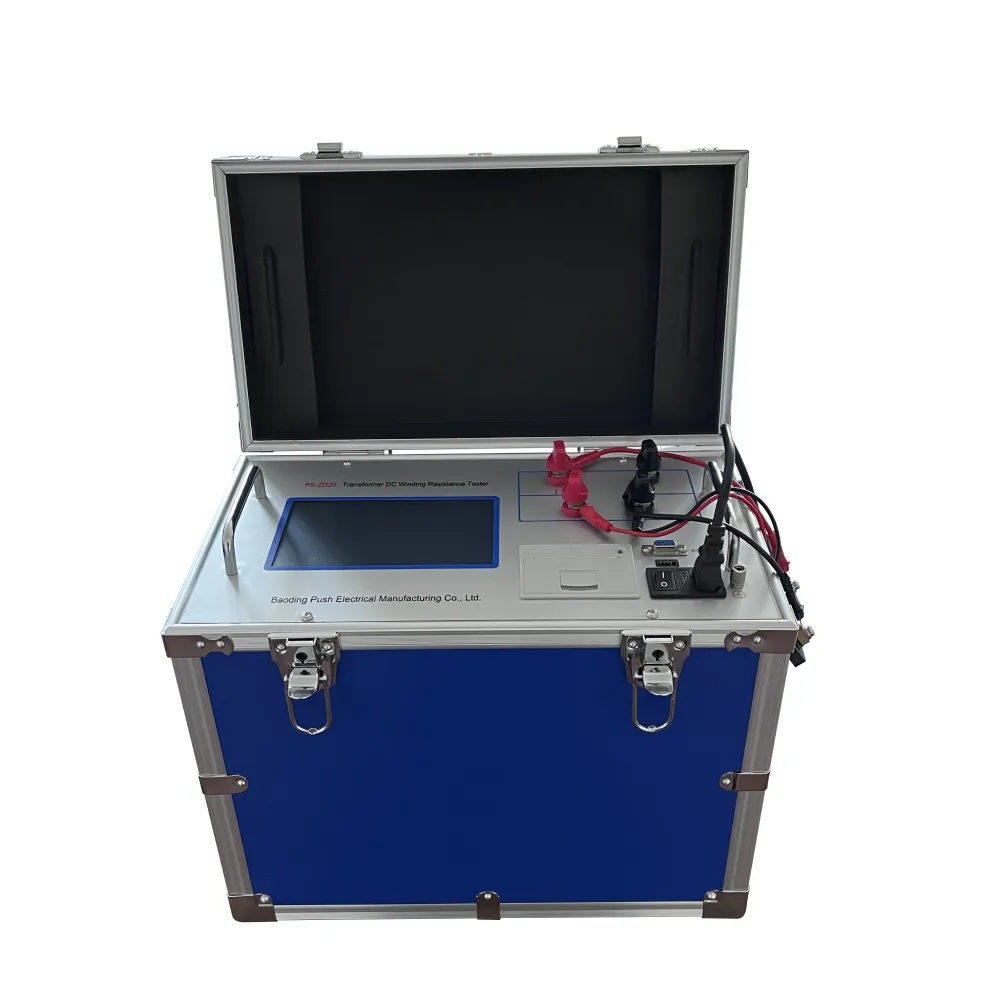
Experience tells us that commissioning a transformer involves myriad tests such as insulation resistance, turn ratio testing, and oil quality assessment. However, a few critical tests are frequently bypassed. One primary omission is the power frequency withstand test. This test, though crucial during manufacturing, is sometimes not re-conducted after installation. The reasoning behind this is often a misjudgment regarding the transformer's factory condition being unaltered during transport and installation, which is not always the case.
Another test that is not routinely executed is the partial discharge measurement. Despite its importance in predicting the longevity and reliability of the transformer, it’s often left out due to the requirement for specialized equipment and expertise. Partial discharges within the insulation can be indicative of defects or deterioration, hence overlooking this test can result in unexpected failures.

Furthermore, acoustic emission testing is another critical assessment that typically doesn't make the cut during on-site installations. This non-intrusive method can detect potential faults by identifying sound waves generated by internal discharges or mechanical issues. The lack of awareness and understanding of the benefits of this test contribute to its infrequent use.
while installing transformer which tests are not performed
From a professional standpoint,
it’s essential to address why these tests are sidelined. Expertise in the field suggests that time constraints, budget limitations, and a lack of local availability of specialized equipment often play significant roles. Transformers are complex, high-ticket items, and the upfront cost pressures can lead stakeholders to minimize perceived 'unnecessary' expenditures.
Addressing these gaps involves fostering an authoritative approach to transformer installations. It necessitates educating stakeholders on the long-term cost benefits of comprehensive testing. For instance, while major failures are rare, they can incur massive downtime and repair costs. By investing in these overlooked tests, organizations can ensure higher reliability and efficiency, ultimately contributing to cost savings and reputational integrity.
Trust in the process is built through rigorous adherence to complete testing protocols. Creating documentation that highlights the necessity and benefits of each omitted test can aid in building transparent procedures. Engineers and project managers should advocate for an all-encompassing testing regime as part of the standard installation procedure.
In conclusion, while it might be tempting to skip certain tests during transformer installations to save time or resources, the potential risks involved call for a more meticulous approach. Prioritize the inclusion of power frequency withstand tests, partial discharge measurements, and acoustic emission testing in your standard operational protocols. This attention to overlooked tests not only enhances the operational lifespan of transformers but also fortifies the reliability and safety commitments made to clients and stakeholders. By implementing a thorough testing regimen, you lay the foundation for trusted and authoritative industry practices.