In electrical engineering, the dielectric resistance test holds a fundamental place in ensuring the safety and functionality of electrical equipment. This test, which measures a material's capacity to resist electric current and act as an insulator, is essential for evaluating electrical insulation systems across numerous industries. The comprehensive understanding and implementation of dielectric resistance testing require an intersection of hands-on experience, technical expertise, authoritative standards, and an unwavering commitment to trustworthiness.
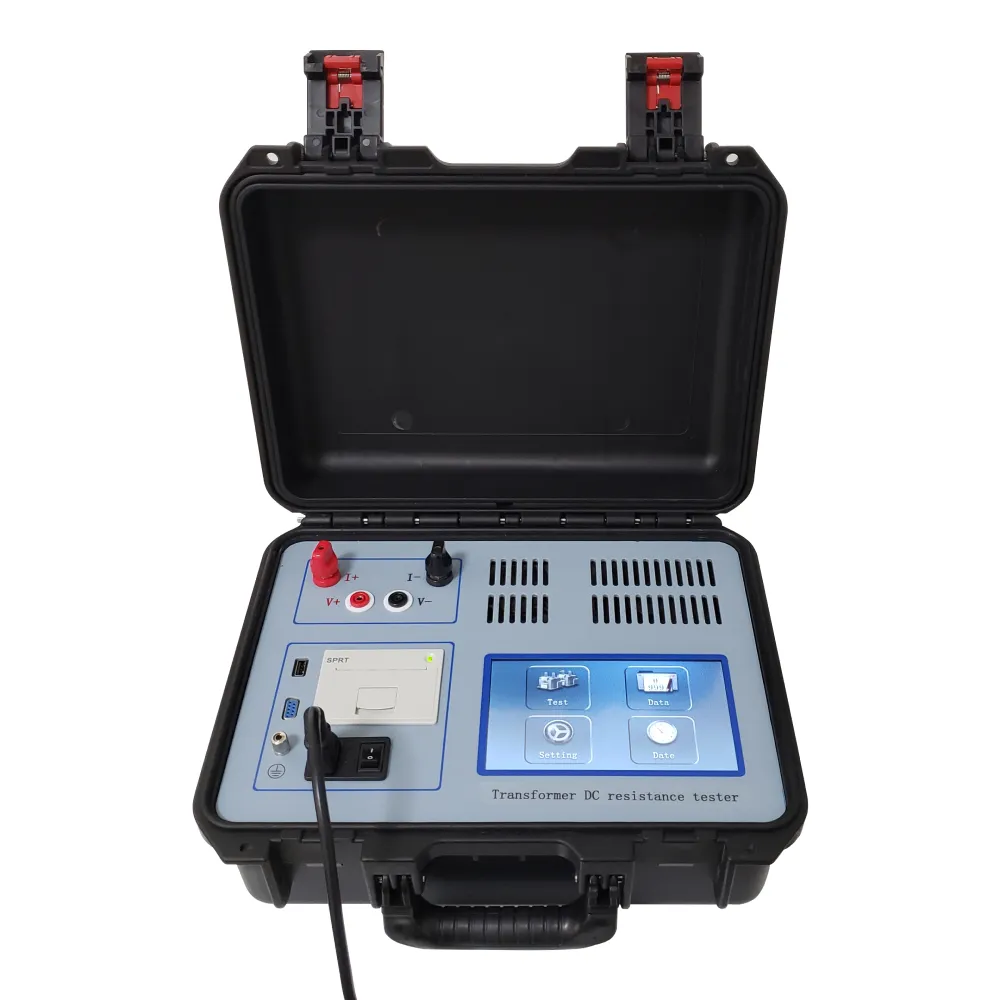
Dielectric resistance tests serve a critical role in preventive maintenance, mitigating the risk of electric failures. Industries reliant on heavy machinery, like manufacturing or power generation, use these tests to predict potential breakdowns. Machines operating beyond their dielectric threshold can experience insulation failure, potentially leading to costly downtimes and hazardous environments. Over the years, seasoned engineers have accumulated extensive experience in conducting these tests, refining techniques to improve precision and reliability in results.
Professionals who specialize in dielectric testing leverage sophisticated instruments and methodologies. Equipment such as megohmmeters and insulation resistance testers are employed to quantify the resistance value of insulating materials. The results, measured in megohms, indicate the quality of the insulation. A higher resistance value suggests better insulating properties, crucial for both alternating and direct current systems. Expertise in handling these complex diagnostic tools is necessary, as even slight inaccuracies can compromise the overall assessment of electrical health.
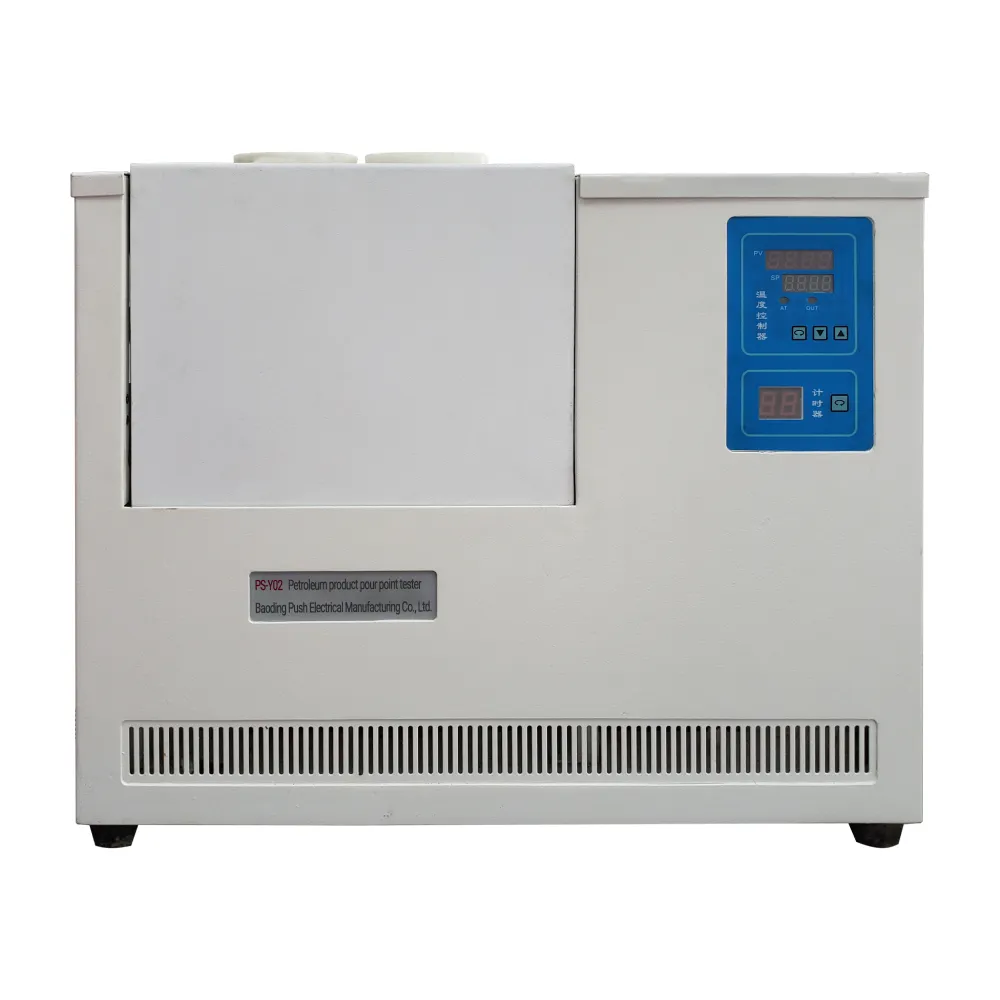
Authoritative bodies, like the IEEE (Institute of Electrical and Electronics Engineers) and IEC (International Electrotechnical Commission), set the industry standards for dielectric resistance testing. Compliance with their guidelines ensures the tests are conducted with the highest level of accuracy and safety. Their documentation provides a comprehensive framework, detailing procedures, equipment specifications, and risk management strategies. By adhering to these standardized protocols, professionals reinforce their authority and credibility in the field, gaining trust from clients and stakeholders.
dielectric resistance test
When it comes to trustworthiness, the process cannot overshadow the ethics of testing. Engineers must ensure test environments are safe and conducive to accurate data collection. Transparency in reporting is paramount—clients need clear, understandable interpretations of test results to make informed maintenance decisions. Moreover, it’s crucial that testing firms maintain independence and impartiality, as biased results can lead to disastrous consequences both financially and operationally.
In recent developments, dielectric resistance tests are increasingly integrated with digital technology, enabling remote monitoring and predictive analytics. Smart testing equipment now offers real-time data transmission and analysis, providing industrial players with the means to anticipate equipment issues before they escalate into emergencies. Seasoned experts harmonize traditional methods with these advanced technologies, enhancing reliability without compromising traditional testing integrity.
In summary, the dielectric resistance test is a cornerstone in electrical maintenance and safety protocols. With a combination of profound expertise, adherence to authoritative guidelines, and unwavering commitment to transparent operations, professionals in this field significantly contribute to safer electrical environments. As industries continue to evolve, so too will the methodologies and technologies underpinning dielectric resistance testing, ensuring its relevance and critical performance in industrial maintenance.