Transformers are critical components in electrical infrastructure, responsible for voltage regulation and efficient power distribution. Ensuring their reliability and performance is pivotal to avoid costly breakdowns and ensure safety. One significant method of verifying their integrity and functionality is the pressure test of transformers. This process evaluates the mechanical strength, leak-proof nature, and overall structural integrity of transformer tanks and associated components.
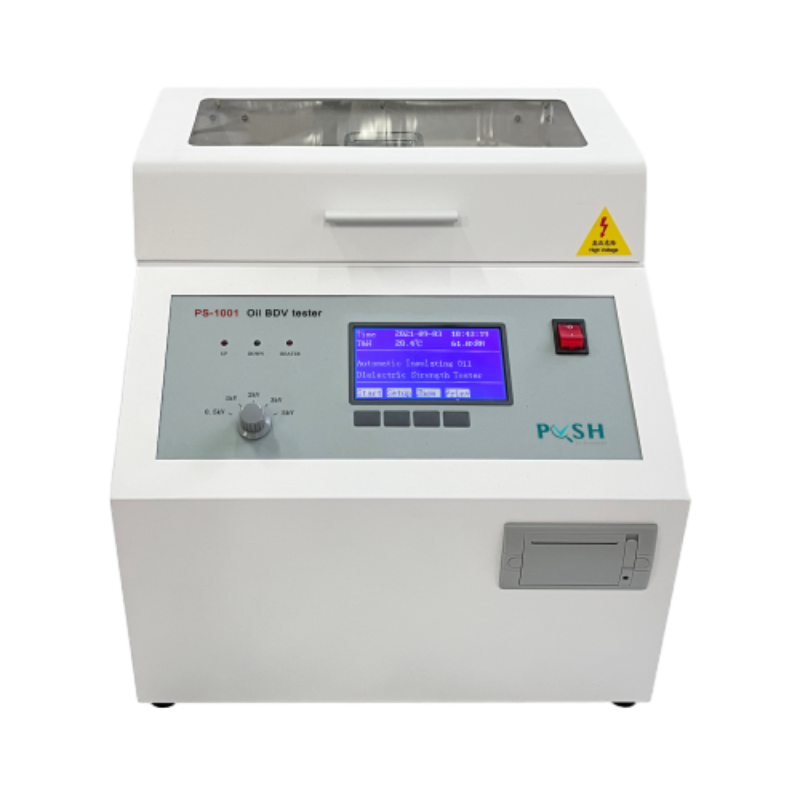
A pressure test of a transformer generally involves the application of gas or liquid pressure to ascertain the robustness of the transformer’s design and fabrication. While the overarching goal is straightforward, the execution requires specific expertise, precise instrumentation, and a methodical approach.
Here’s a detailed dive into the nuances of transformer pressure testing
1. Understanding Pressure Test Types
Various methods can be employed when pressure testing a transformer, primarily governed by the nature and design of the transformer and its application. Commonly, these include hydrostatic tests and pneumatic tests. Hydrostatic testing involves filling the transformer with a fluid – typically water or oil – and pressurizing it to check for leaks or structural deficiencies. Pneumatic testing, on the other hand, uses air or another gas. Each method offers its own set of advantages. The hydrostatic test is generally safer due to the incompressible nature of liquids, whereas pneumatic testing can be more revealing under certain conditions due to differential detection.

2. Equipment and Safety Measures
Conducting a pressure test with high precision necessitates specialized equipment such as pressure gauges, pumps, and sealing mechanisms. A critical aspect of the process is establishing correct safety protocols; given the pressures involved, a failure could lead to catastrophic damage. Thus, testing areas should be cordoned off, with personnel equipped with safety gear and trained in emergency procedures.
3. The Executing Process
Before initiating the test, it’s imperative to inspect the transformer externally for any visible defects or wear and tear. The transformer is then either filled with the test medium — in the case of hydrostatic testing — or sealed airtight for pneumatic testing. Pressure is gradually increased to the desired level, typically above operational levels to factor in safety margins. The equipment should be meticulously monitored throughout to identify any drop in pressure indicating leaks or structural weaknesses.
pressure test of transformer
4. Data Collection and Interpretation
Pressure testing is not just about verifying pass or fail but also entails detailed data collection. Pressure data can provide insights into the weld integrity, seam strength, and detection of subtle fault lines. An experienced engineer could interpret these nuanced readings to predict potential points of failure, contributing to preventative maintenance strategies.
5. Post-Test Analysis
After completing the test, it is essential to methodically decompress and remove the testing media, followed by a thorough inspection to assess any impacts the test may have had on the structure. Verification through non-destructive evaluations such as ultrasound or radiography can provide additional reassurance of structural resilience.
6. Regulatory and Compliance Perspectives
Pressure testing, while technically demanding, aligns with broader regulatory compliance and certification frameworks. Meeting standards such as IEEE C57.12 for liquid-immersed transformers or equivalent regional guidelines reinforces a transformer’s legitimacy and suitability for deployment. Compliance not only ensures quality but also enhances the transformer's marketability in industries prioritizing reliability and safety.
7. Trust and Authority Through Expertise
Finally, the credibility of pressure testing as a sound practice hinges on the expertise of those conducting it. Therefore, employing certified professionals with proven track records in transformer testing enhances confidence in results, fostering trust among stakeholders such as manufacturers, operators, and regulatory bodies.
Pressure testing of transformers represents a vital intersection of engineering proficiency, safety mandates, and operational reliability. In an era where electrical resilience is foundational to daily life, mastering techniques like pressure testing is indispensable, propelling not only industry standards but also public assurance. This comprehensive understanding of transformer integrity fosters robust networks that are crucial to modern infrastructural demands.