Ensuring the optimal performance and longevity of transformers is crucial, not only for the reliability of electrical systems but also for the safety of operation management. Transformer oil plays a pivotal role in this, serving both as an insulator and a coolant. Regularly checking transformer oil levels is paramount for maintaining efficiency and preventing costly breakdowns.

Checking the transformer oil level is akin to examining a car's engine oil before hitting the road. It allows engineers to detect possible leaks and ensure the transformer is operating at peak efficiency. Transformer oil serves as a barrier to electrical faults and a coolant to dissipate heat from the core and windings. Thus,
maintaining the correct oil level is essential.
Understanding the consequences of low transformer oil levels highlights the importance of routine checks. When oil levels decrease, the risk of electrical discharges increases, which can lead to insulation failures or even cause the transformer to overheat. Such incidents may necessitate expensive repairs or replacements, impacting the operational workflow considerably.
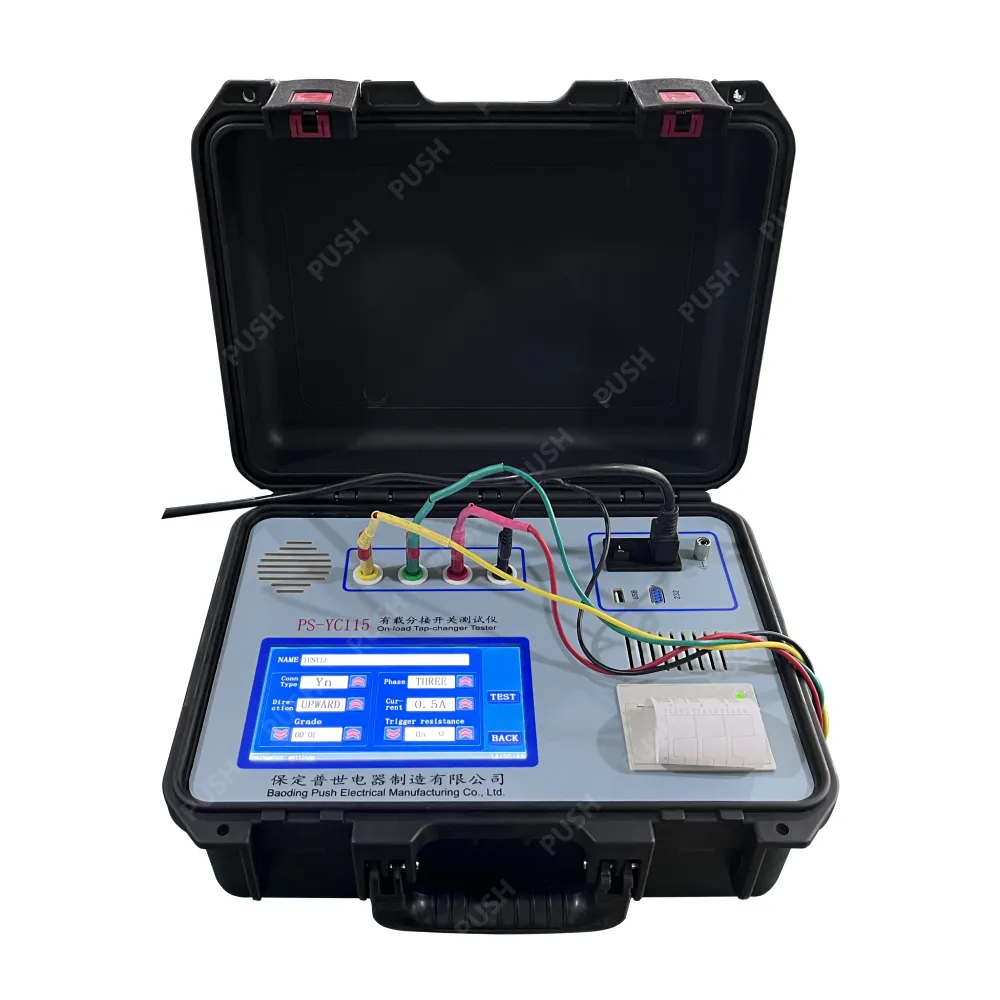
One of the most authoritative methods to check the oil level involves periodic inspections using through-view glasses known as oil gauges, which are typically affixed to the transformer tank. These gauges allow engineers to visually confirm the liquid level, gauging it against marked indicators that show the safe range. However, simply relying on visual assessments can be misleading due to ambient temperature variations that cause oil expansion or contraction. Therefore, it's recommended to perform checks under standardized temperature conditions to ensure accuracy.
Employing automated methods, like using sensor-based oil level monitoring systems, brings enhanced precision to the process. These systems use ultrasonic or capacitive sensors to provide real-time data on oil levels, allowing for prompt corrective measures. Thus, investment in such systems can actually save costs significantly by preventing downtime and mechanical failures.
transformer oil level check
Industry experts advocate for scheduling transformer oil level inspections as part of preventative maintenance programs. Conducting these checks on a monthly or quarterly basis, depending on the operational demands and environmental conditions, is advised. When performing inspections, it’s important to couple oil level assessments with oil quality checks to ensure the oil retains its insulating properties and hasn't degraded over time.
To enhance expertise, training on oil level assessment and the interpretation of gauge readings is essential for personnel involved in transformer maintenance. This training should include understanding the oil's role in transforming operations and learning the nuances of level fluctuations relative to different stressors, such as temperature changes and load variations.
Maintaining trustworthiness in the management of transformer systems comes with adhering to industry standards and practices. Utilizing high-quality oil and accredited equipment, well-documented procedures, and ensuring robust data recording of oil level checks builds confidence in operational integrity.
In essence, maintaining the proper transformer oil level is a fundamental aspect of electrical system reliability and safety. Regular, accurate measurement prevents potential damages and extends the lifespan of the equipment. By implementing best practices and leveraging advanced technologies, businesses can ensure their transformers operate efficiently, safeguarding both investments and personnel. This vigilant approach builds superior expertise, authority, and trustworthiness, aligning with the esteemed benchmarks of operational standards and consumer expectations.