Insulation power factor testing is a crucial process to evaluate the condition of electrical insulation. It measures the dielectric losses in insulation, which helps determine the capability of electrical equipment to withstand service voltages and other stresses. This testing method is crucial for ensuring the safety and efficient operation of transformers, circuit breakers, capacitors, and other high-voltage electrical equipment.
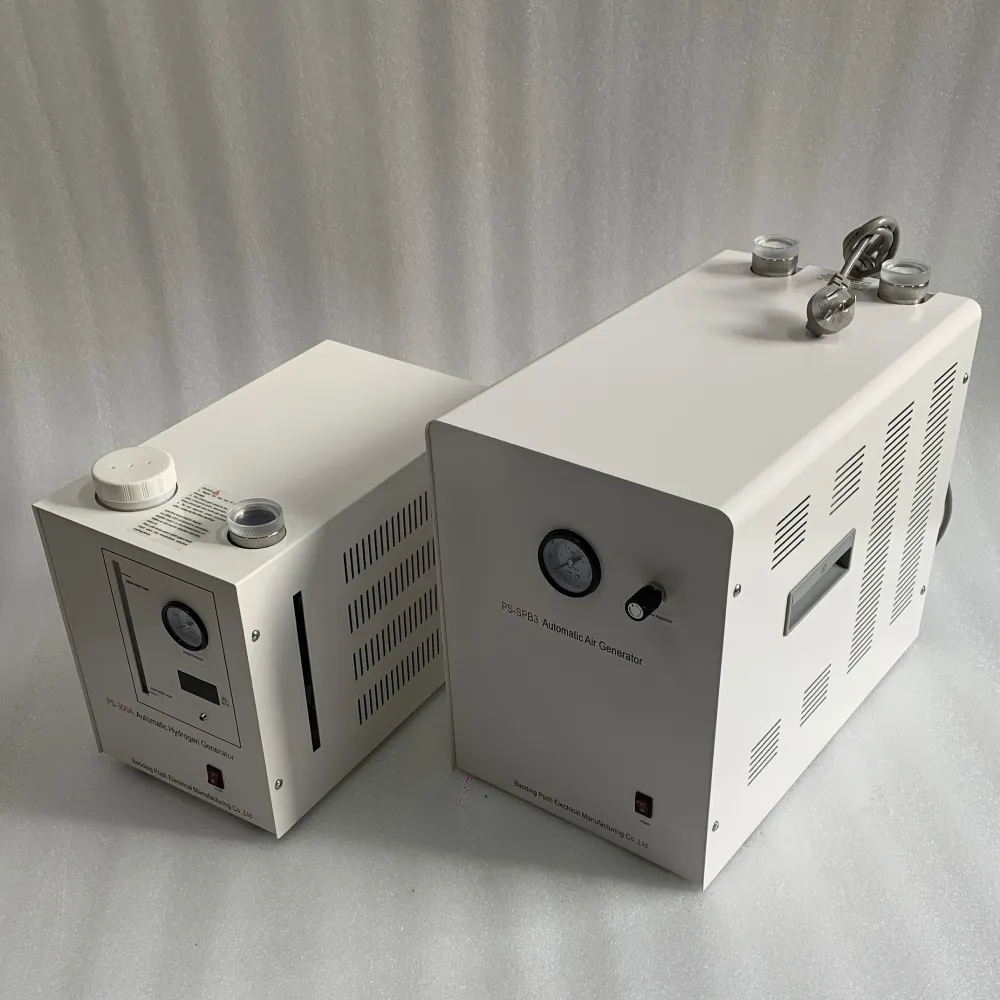
As a seasoned electrical engineer with extensive field experience, I've witnessed firsthand the vital role that insulation power factor tests play in prolonging the lifespan of electrical apparatus. At its core, the insulation power factor test measures the ratio of resistive current to capacitive current, offering insights into the dielectric's integrity. Higher power factor readings typically indicate deteriorating insulation, which can lead to catastrophic failures if left unaddressed.
One fundamental aspect of insulation power factor testing is its ability to detect various insulation problems, including moisture content, dirt accumulation, aging, and thermal deterioration. In my practice, I've often found that moisture is a common culprit in insulation degradation. Regular insulation power factor tests can identify the sources of moisture ingress, allowing timely interventions such as improving seals or dehydrating the equipment through vacuum or heat treatments.

The procedure for performing an insulation power factor test requires attention to detail and a strong understanding of both the equipment being tested and the environmental conditions. When preparing for the test, it is essential to ensure that the equipment is de-energized and properly grounded to avoid any safety hazards. Furthermore, tests should ideally be conducted during stable temperature conditions as fluctuations can affect the readings. I've learned that thorough preliminary inspections should be conducted to identify any visible signs of damage or contamination.
Once the equipment is set up for testing, using a power factor test set, such as a bridge or a tan delta kit, can measure the insulation's power factor accurately. Interpreting these results necessitates an understanding of baseline metrics for healthy equipment compared to industry standards. Through countless tests, I've come to rely on historical data from previous tests of the same equipment as well as manufacturer specifications, ensuring that any deviation from expected results is appropriately contextualized.
insulation power factor test
Proficiency in insulation power factor testing also involves an understanding of how different pollutants and operational conditions influence readings. For example, equipment exposed to industrial pollutants or salt-laden air will naturally exhibit higher power factor readings due to contamination. My experiences have taught me that implementing a robust maintenance and cleaning routine can mitigate these influences, leading to more accurate assessments.
Trust in the results of insulation power factor tests hinges on the reliability of the test equipment and the expertise of the technician conducting the test. It is pivotal to ensure that the test equipment is regularly calibrated and maintained. In my role, I've championed rigorous training programs for technicians, emphasizing the need for both theoretical knowledge and hands-on practice. This approach enhances the reliability of test results, fostering confidence in the subsequent maintenance actions.
Moreover, the authoritativeness of insulation power factor testing is supported by various regulatory and industry standards, such as those outlined by IEEE and IEC. Complying with these standards not only affirms the credibility of the tests but also ensures that the methodologies employed are up to date with technological advancements and industry best practices.
In conclusion, insulation power factor testing stands as a testament to the integration of experience, expertise, authority, and trust in the realm of electrical equipment maintenance. It provides a proactive approach to detecting potential failures, ultimately safeguarding electrical systems and optimizing their performance. Familiarity with this testing not only enhances the lifespan of equipment but also builds a foundation of reliability and safety—a goal every electrical engineer and technician strives to achieve.