DC insulation testers, essential instruments in the electrical and electronics industries, play a pivotal role in ensuring electrical systems' safety and efficiency. Offering an unparalleled perspective grounded in decades of expertise, this article delves into the key features, applications, and best practices surrounding these indispensable tools.

A DC insulation tester, also known as a megohmmeter, is designed to measure the resistance offered by insulating materials within electrical systems. High resistance indicates good insulation, while low values suggest potential failures. This critical process helps prevent electrical accidents, equipment failures, and operational downtime.
The expertise required to select the right DC insulation tester is pivotal. Not all testers are created equal, and understanding their specifications is vital. Key features to consider include the test voltage range, measurement accuracy, and the device's capability to store data. Test voltage ranges can vary significantly from as low as 50 volts, ideal for delicate electronics, up to 10,000 volts for industrial applications. The precision of measurements, often displayed digitally for clarity, is crucial, especially in situations where minute differences can signal significant issues.
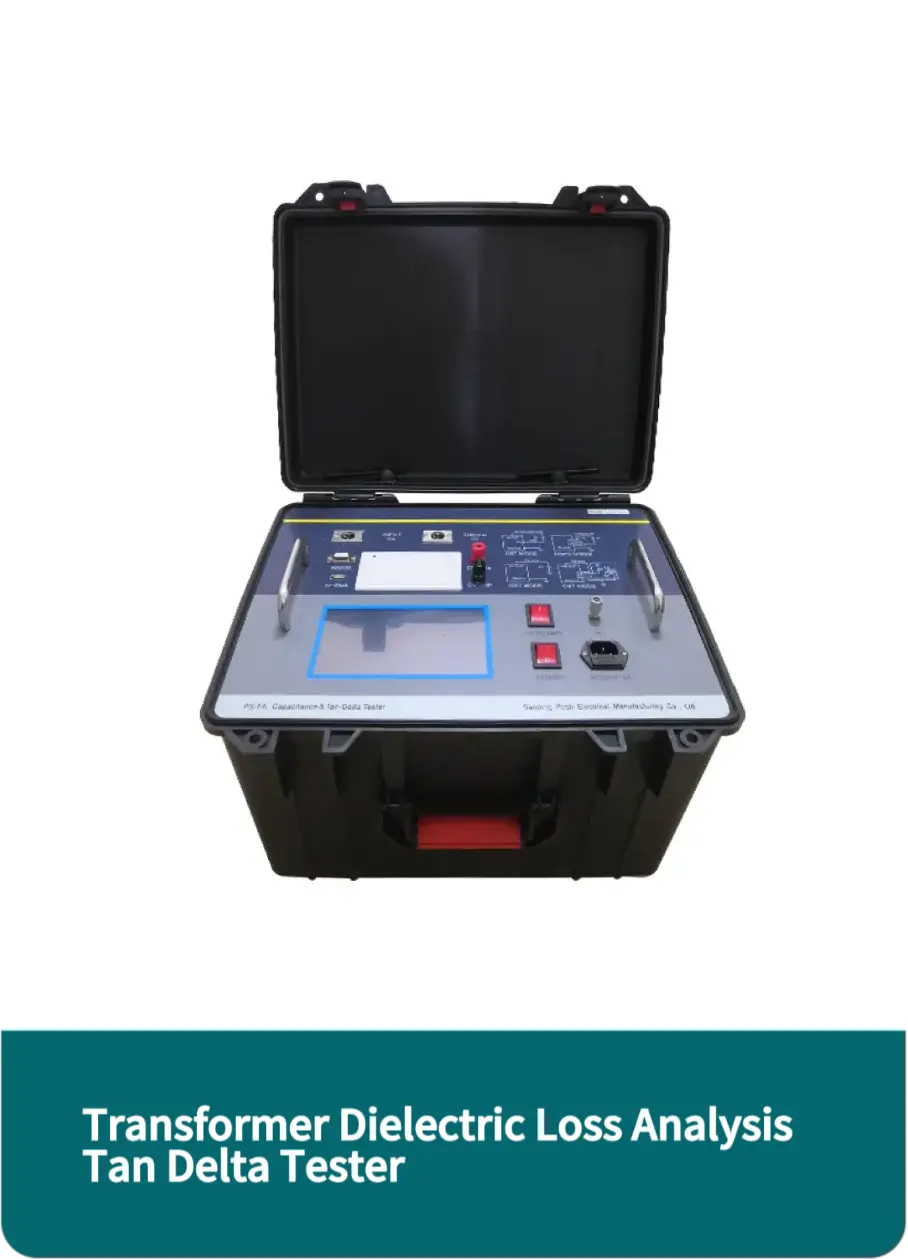
A hallmark of these testers is their ability to provide diagnostic insights. Advanced models offer PI (Polarization Index) and DAR (Dielectric Absorption Ratio) measurements, giving a deeper understanding of insulation conditions over time. These indices can signal moisture ingress, thermal degradation, or other aging-related issues, allowing for proactive maintenance.
Ensuring the reliability of electrical installations necessitates an authoritative approach to testing. Periodic testing with DC insulation testers serves not only to validate the integrity of the insulation but also to extend the lifespan of the electrical systems. A well-documented regime, where results are compared over time, can highlight trends indicating gradual insulation degradation.
Experienced electrical engineers advocate for the integration of DC insulation testing into regular maintenance schedules. Its effectiveness is multiplied when complemented by other testing methods such as thermal imaging and ultrasonic testing, providing a comprehensive view of system health.
dc insulation tester
The trustworthiness of a DC insulation tester is often linked to its compliance with international standards such as IEC 61557-2 or IEEE 43. These standards ensure that the devices perform reliably under varied conditions, providing users confidence in their assessments. Choosing devices from reputed manufacturers with a proven history in the industry further enshrines trust.
Real-world applications of DC insulation testers are vast. In industrial settings, they are used to test motors, transformers, and cables. In critical environments like hospitals or data centers, where uninterrupted power supply is non-negotiable, their role in predictive maintenance is indispensable. Moreover, during the commissioning phase of new installations, these testers assure stakeholders of the system's readiness.
Safety cannot be overstressed when using DC insulation testers. Operators must be proficient, understanding not only how to use the equipment but also the implications of the readings. Proper personal protective equipment (PPE) and adherence to safety protocols are non-negotiable, ensuring that the benefits of these testers do not come at the cost of human safety.
In an era where digitization is sweeping across all facets of life, many DC insulation testers now offer advanced features such as Bluetooth connectivity and integration with data management software. These capabilities streamline the process of logging, retrieving, and analyzing test results, enhancing the user's ability to make data-driven decisions.
Ultimately, the impact of DC insulation testers on maintaining high standards of electrical safety and efficiency is immense. With the authority gathered through decades of use and evolution, these tools remain indispensable to engineers and technicians dedicated to safeguarding our increasingly electrified world. Their strategic use, informed by expertise and supported by continuous learning and adaptation, ensures they remain at the forefront of electrical diagnostic equipment.