Power transformers are critical components in electrical grids, ensuring efficient energy transfer and stability across different systems. To maintain their reliability and maximize their lifespan, regular testing is essential.
Different types of transformer testing provide unique insights into their condition, helping to prevent unexpected failures. This article delves into various testing methodologies for transformers, emphasizing their importance and underlying technical prowess.
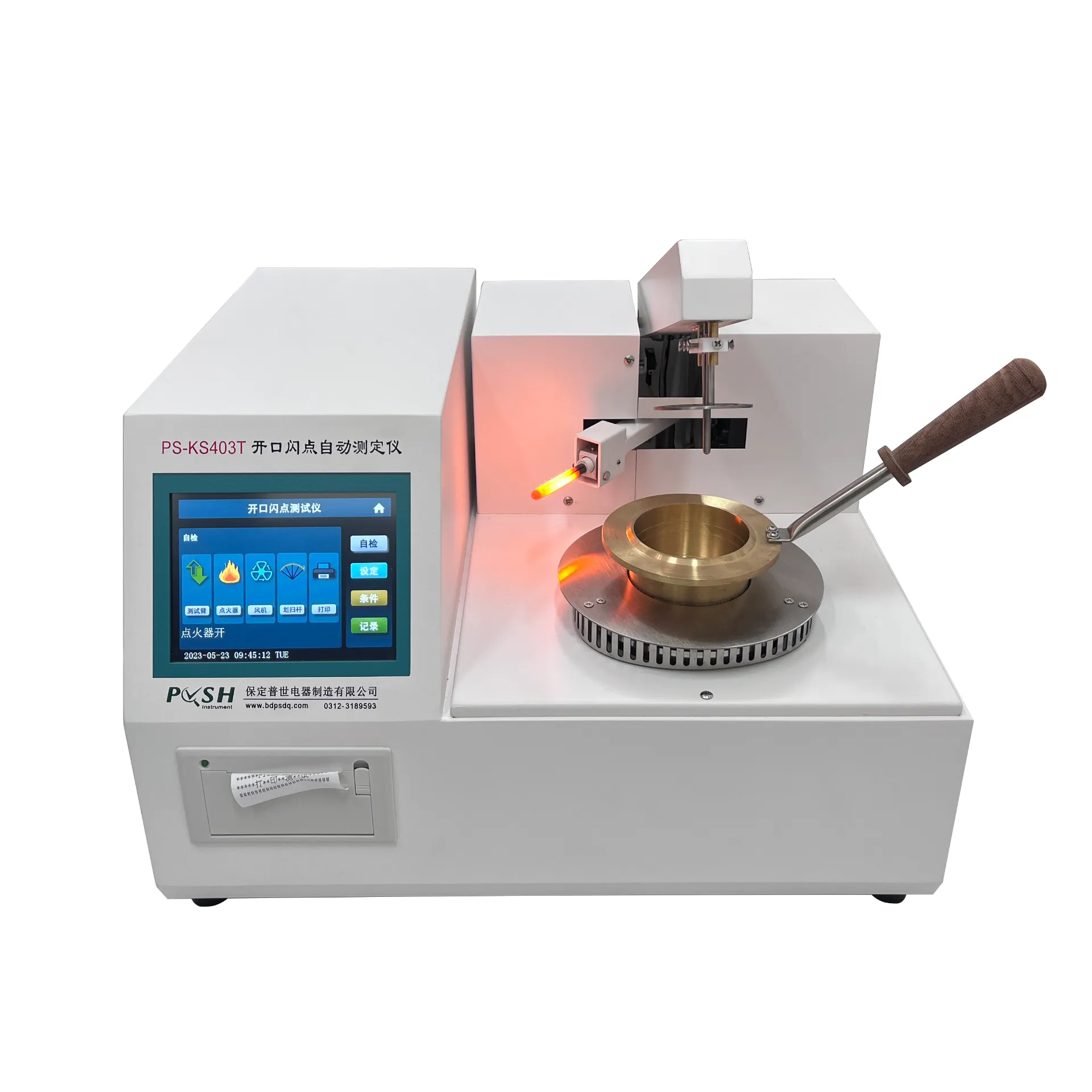
Transformer testing can be broadly categorized into routine tests and special diagnostic tests. Routine tests are usually performed at the manufacturing stage and during periodic maintenance, including a series of standardized checks that ensure a transformer's basic functionality and safety. These tests include insulation resistance tests, turns ratio tests, winding resistance tests, and more.
The insulation resistance test is vital to measure the effectiveness of a transformer's winding insulation. This test ensures that there isn't an unintended current path between windings and the transformer's core or body. It uses an insulation resistance tester or a megohmmeter to apply a high DC voltage, often between 500V and 10kV, across the insulation and measure the resistance. Ensuring high insulation resistance is critical for operational safety and efficiency.
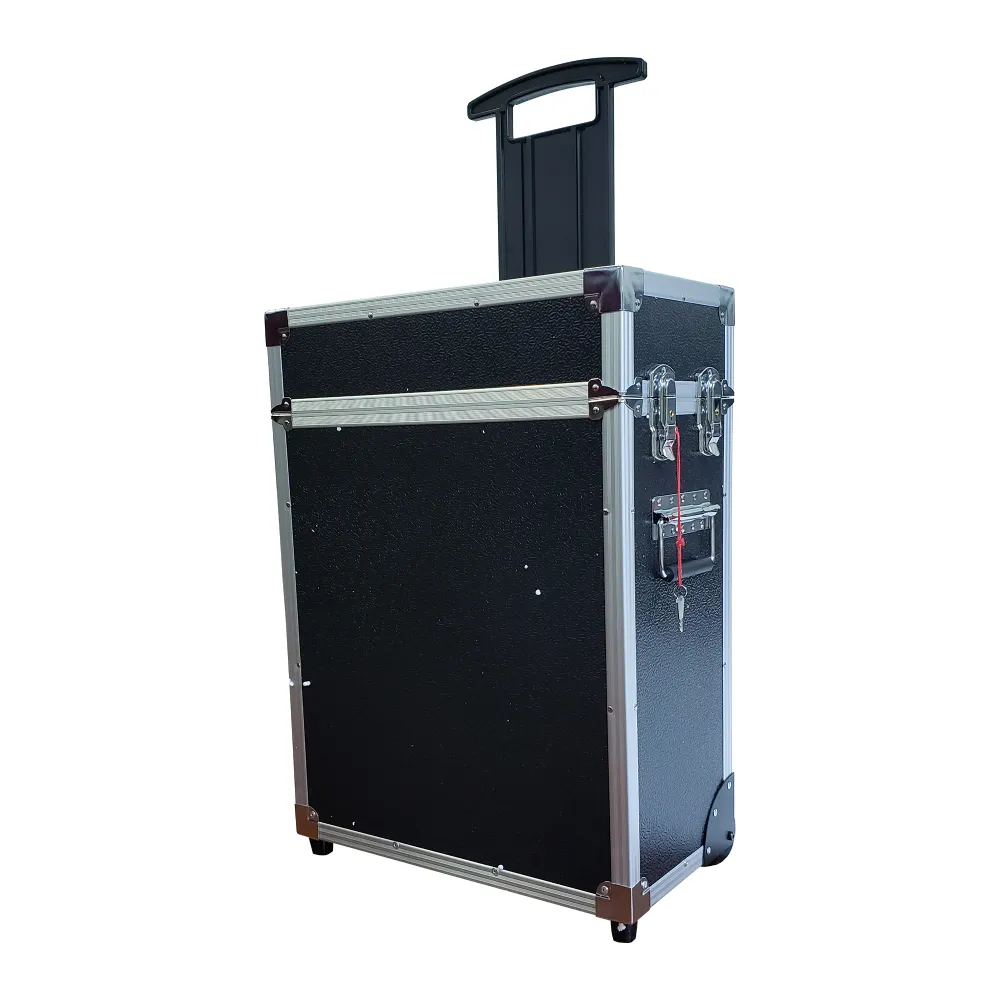
Turns ratio tests are conducted to verify that the transformer's windings have been connected correctly and are operational as designed. This test is crucial because even a small variance in the turns ratio could lead to inefficient voltage regulation or excess heat generation. Equipment used for this includes a ratio meter, which applies a smallervoltage to the primary winding and measures the resultant voltage in the secondary winding.
Winding resistance testing is another essential routine test. It detects issues like loose connections, broken strands, or contact problems in tap changers. The test involves passing a DC current through the winding and measuring the voltage drop, using Ohm’s Law to calculate the resistance. Significant deviations from expected resistance values can indicate underlying issues requiring immediate attention.
For transformers that have been in service for an extended period, diagnostic testing is critical to assess their operational health beyond the standard routine tests. One popular diagnostic test is the frequency response analysis (FRA), which evaluates a transformer's structural integrity by measuring the transformer's response to a range of frequencies applied across its windings. This test can reveal mechanical displacements within the windings, often caused by events like short circuits or physical shocks.
different types of transformer testing
Dissolved gas analysis (DGA) is another advanced diagnostic technique, pivotal in identifying potential faults within the transformer. Transformers may exhibit gradual deterioration through dielectric breakdown or thermal degradation, releasing gases within the oil. DGA detects these gases and analyzes their concentration to identify potential electrical faults like arcing or overheating at an early stage.
Partial discharge (PD) testing is crucial for detecting localized defects within transformer insulation. PD testing measures micro pulses or discharges during a breakdown period. Advanced PD test equipment can identify the location and severity of insulation defects, which is vital for maintenance planning and preventing catastrophic failures.
Moreover, advanced technologies like infrared thermography and acoustic emission testing offer additional layers of diagnostic capability. Infrared thermography detects hot spots on a transformer’s surface that could indicate internal issues, while acoustic emission testing identifies and locates defects based on the sound waves generated by partial discharges, structural stresses, or mechanical defects.
In addition to these tests, modern transformers are often equipped with online monitoring systems that utilize sensors to provide real-time data analysis. These systems help in constant monitoring of parameters such as temperature, load pressure, and oil quality, offering predictive insights and enabling condition-based maintenance strategies.
By combining routine and diagnostic testing methods, utilities and operators can ensure that transformers continue to operate efficiently, minimizing the risk of unexpected failures. Expertise in selecting and interpreting the results from these tests is crucial for maintaining the integrity and performance of power systems. Authoritative guidelines and standards, such as those from the IEEE and IEC, provide a framework for conducting these tests, further enhancing trustworthiness in testing outcomes.
Overall, transformer testing encompasses a blend of foundational and advanced techniques, each serving its role in safeguarding electrical infrastructure. The careful application of this expertise allows operators not only to maintain system reliability but also to foresee potential issues and manage them proactively, creating a robust power network that meets both current and future demands.