Testing a transformer with a multimeter is an essential skill for technicians and engineers, ensuring electrical systems function correctly and safely. Transformers are pivotal in altering voltage levels for various applications, from small-scale electronics to large industrial plants. Understanding how to accurately test a transformer can prevent failures and improve performance.

Transformers work on the principle of electromagnetic induction, consisting of primary and secondary coils. Testing involves checking their resistance and ensuring there’s proper continuity. A multimeter, a versatile tool that measures voltage, current, and resistance, is indispensable in this process.
Firstly, safety is paramount. Before testing, disconnect the transformer from any power source. This preventive measure protects not just the tester, but also the equipment from accidental damage caused by electrical currents. Moreover, use insulated tools and wear protective gear, such as rubber gloves and goggles, to safeguard against any surprises.
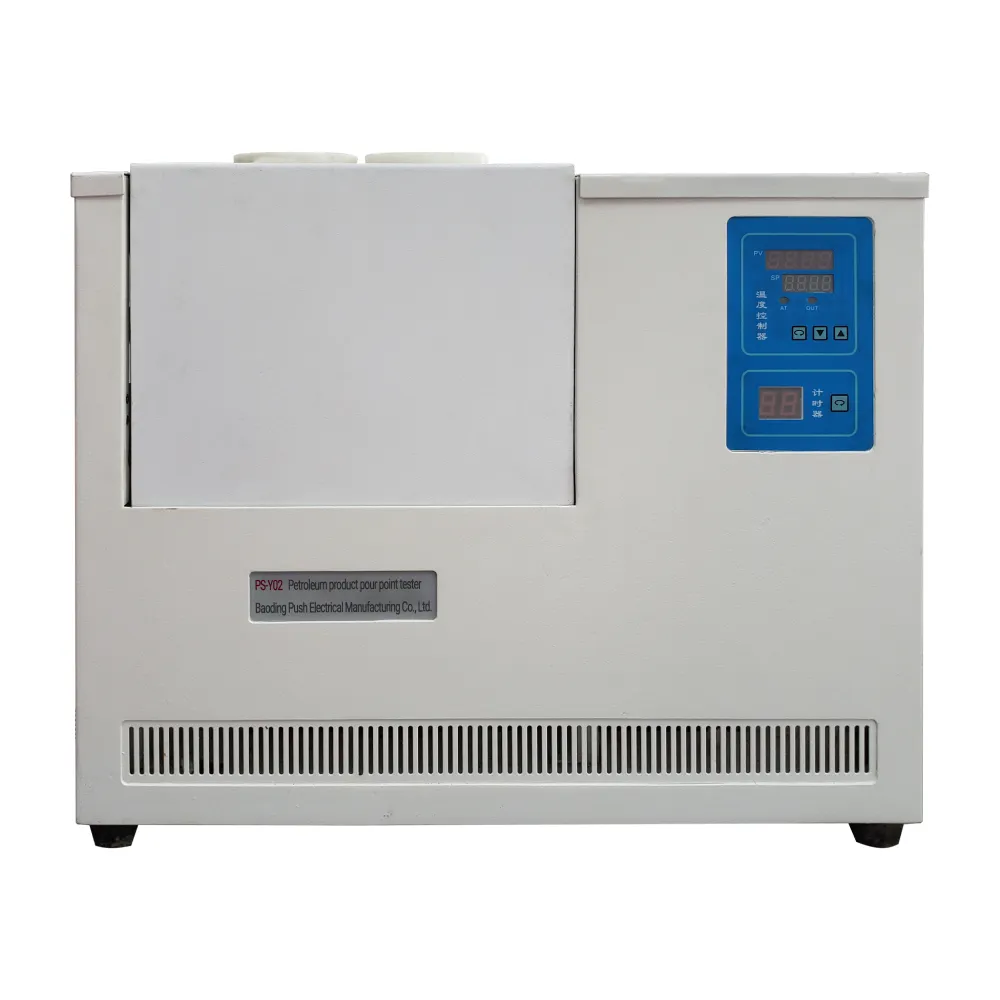
Begin with a visual inspection. Look for physical damage, such as burn marks, corrosion, or damaged insulation. Such indicators might point out faults even before any electrical testing begins. Ensure that the transformer is clean and dry; moisture can affect readings and may be indicative of underlying issues like leakage points.
Set the multimeter to the resistance (ohms) mode. Attach the probes to the primary winding terminals. A good transformer should show a low resistance value typically within a few ohms, suggesting that the winding is intact. A reading of infinite resistance signifies a broken winding, while zero resistance suggests a short circuit.
Both results mean the transformer needs repairing or replacing.
Next, test the secondary winding in the same manner. Compare the readings to the manufacturer’s specifications, which provide a baseline for what's expected. Any deviation might point to an issue needing attention.
test a transformer with a multimeter
After testing resistance, the continuity check comes next. Set the multimeter to the continuity setting and connect the probes similarly. Listen for the beep sound, indicating uninterrupted electrical flow. A silent multimeter suggests discontinuity, helping pinpoint possible breaks.
Voltage testing should be your final step. Reconnect the transformer to a safe and suitable power source, using all necessary safety precautions. Switch the multimeter to voltage mode to check for correct transformer output. Reference this against the expected output voltage as per specifications. A significant deviation could mean internal issues like winding problems or insulation failures.
Documenting each step and the test results is a critical practice. It not only helps in troubleshooting but also becomes valuable data for future reference and analysis. Sharing these details with team members can foster a more knowledgeable workforce.
Beyond just testing, maintaining a transformer enhances longevity and reliability. Keep an eye on those environmental factors like temperature and humidity, as they can accelerate wear and reduce efficiency. Incorporate routine inspections into maintenance schedules, ensuring small problems are tackled promptly before they manifest into larger, costlier issues.
In the evolving landscape of electrical engineering, the ability to efficiently test and diagnose transformer issues empowers professionals. Building on expertise in handling transformers not only saves time and cost but also ensures system stability and safety. Innovative approaches and staying updated with the latest testing technologies further complement this skill set.
Ultimately, having a reliable method to test transformers, combined with experience and expertise, establishes trust in the results. As technology advances, continuously refining these processes is key to maintaining high standards in electrical engineering and ensuring that all systems operate without interruptions.