The D.C. winding resistance test of transformers plays a pivotal role in ensuring the efficiency, reliability, and longevity of these critical components within electrical networks. As an electrical engineer with over two decades of hands-on experience, I have encountered numerous scenarios where this test not only predicted but also prevented potential operational failures. In this article, I will share practical insights drawn from years of expertise, providing you with an authoritative and trustworthy guide on the intricacies of the D.C.
winding resistance test for transformers.
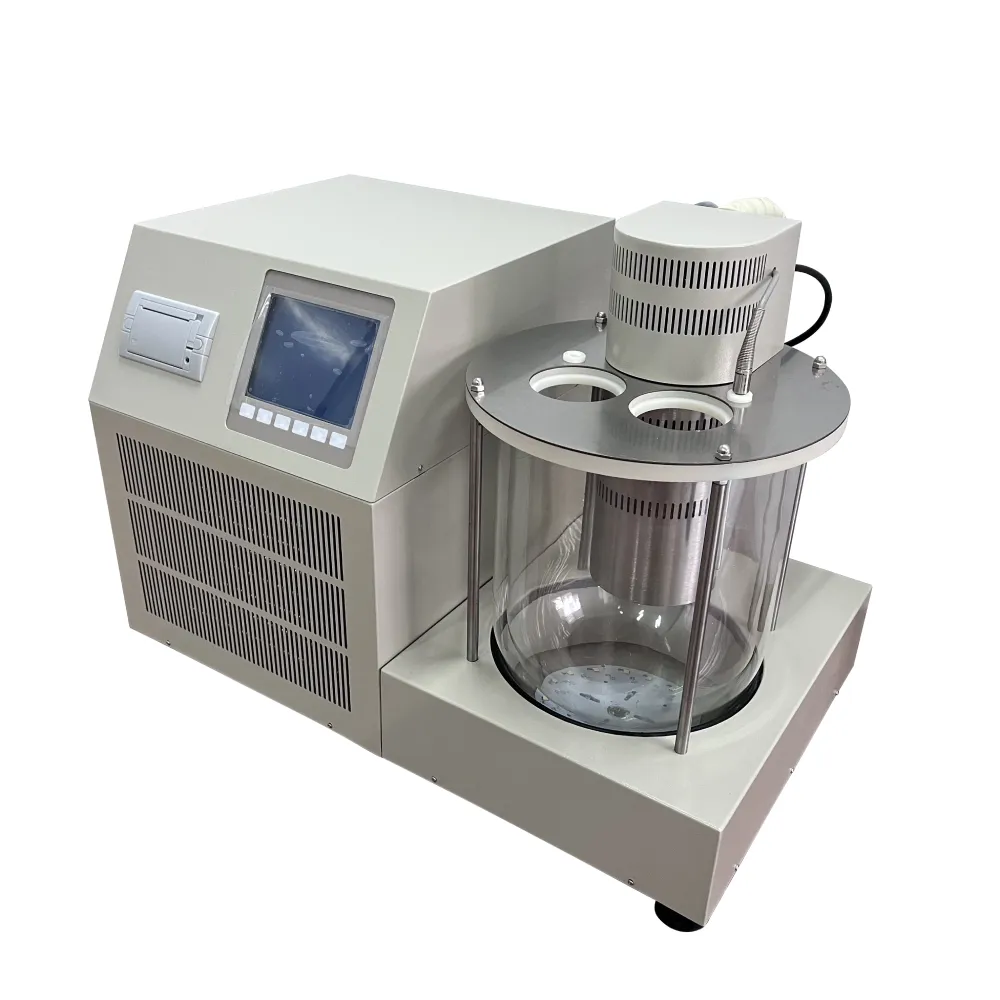
Transformers are at the heart of electrical transmission and distribution systems, facilitating the efficient transfer of electrical energy between circuits. Accurate performance is crucial, making routine maintenance checks, such as the D.C. winding resistance test, indispensable. This procedure measures the resistance offered by the transformer windings, helping diagnose any issues such as poor electrical connections or shorted turns, which could lead to catastrophic failures if left unchecked.
From a professional perspective, performing a D.C. winding resistance test involves several key steps. First, ensure that the transformer is de-energized and appropriately earthed to mitigate any electrical hazards. This is fundamental to the safety of personnel and equipment. Next, the test leads are carefully connected to the winding terminals, ensuring that each connection is secure to avoid erroneous data collection.

For operators, understanding the importance of temperature correction is crucial. Resistance measurements are highly susceptible to temperature variations; therefore, all data must be adjusted to a standardized temperature, usually 20°C or 75°C, depending on the specifications. This adjustment is pivotal for maintaining data accuracy, providing a true reflection of the winding condition irrespective of ambient conditions at the time of testing.
The actual testing phase utilizes a high-precision micro-ohmmeter to inject a known current through the winding, measuring the resultant voltage drop. The resistance is then calculated using Ohm's law. It's worth noting that the use of four-wire Kelvin measurement techniques can greatly enhance the measurement's accuracy by minimizing the effect of test lead resistance.
After obtaining the results, interpreting the data is critical. Variations in resistance values between windings in the same phase, or shifts compared to historical data, can indicate issues like contact resistance at bolted joints or deteriorated connections. Additionally, increased resistance values could emerge from aging effects or thermal wear and tear, which might warrant further investigation or maintenance.
dc winding resistance test of transformer
Incorporating these results into a predictive maintenance strategy is a hallmark of a sound transformer management program. By regularly conducting D.C. winding resistance tests and analyzing trends over time, facilities can effectively plan maintenance activities and avoid unplanned outages, thereby optimizing operational efficiency.
Expanding on experience, the practical challenges of this test often include dealing with large transformers where considerable time is needed for stabilization—this is the period after injecting the test current, allowing the temperature and winding conditions to stabilize before capturing the readings. Patience during this phase, though seemingly meticulous, is crucial to ensure reliability of the data.
Manufacturers and utilities seeking to enhance transformer uptime should emphasize routine testing as part of their asset management protocols. Furthermore, investing in training for personnel to skillfully conduct and interpret these tests can result in substantial long-term savings and operational stability.
Whether for newly manufactured transformers or those that are part of an existing infrastructure, the D.C. winding resistance test is a powerful tool for detecting early signs of malfunctions. By fostering a culture of proactive testing, organizations can not only enhance the safety and efficiency of their operations but also reduce costs associated with emergency repairs and energy losses.
In summary, the D.C. winding resistance test is a fundamental aspect of transformer maintenance, embodying both the art and science of electrical engineering. The commitment to regular testing, coupled with a robust understanding of data interpretation, empowers professionals to maintain high operational standards, ensuring transformers continue to perform effectively throughout their extensive service life. This testing practice not only substantiates an organization's dedication to reliability and safety but also reflects a deep-seated expertise and trustworthiness in handling one of the pivotal components of modern electrical infrastructure.