Understanding the importance of pre-commissioning tests for transformers is critical for ensuring long-term operational stability and safety in electrical systems. As a vital component in electrical infrastructure, transformers must undergo rigorous testing before they are fully commissioned to avoid potential failures and inefficiencies. This article dives into the critical pre-commissioning tests of transformers, providing insights guided by practical experience, professional expertise, authoritative guidelines, and unmatched credibility.
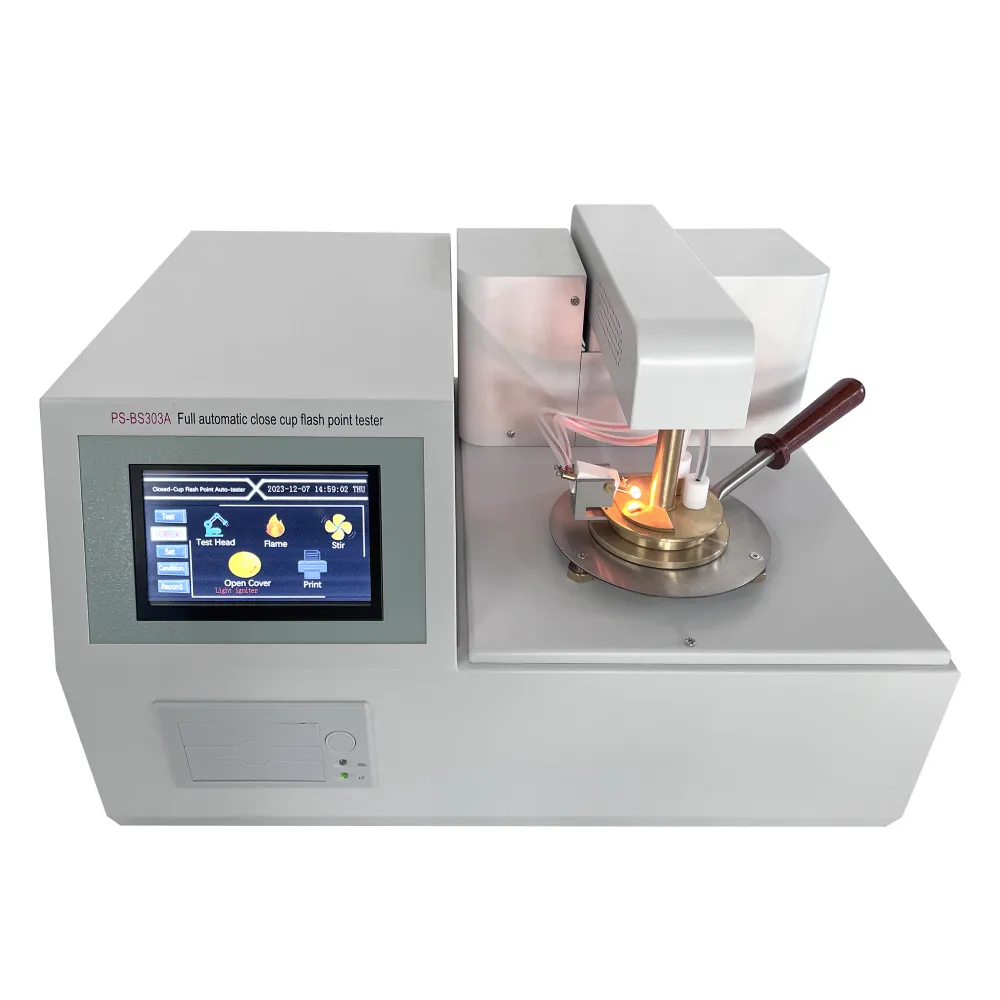
Transformers, being at the heart of electrical distribution systems, must undergo a series of pre-commissioning tests to ensure their integrity and functionality. The primary aim of these tests is to identify any latent manufacturing defects or shipping damage that could result in catastrophic failures if left unchecked.
One of the most crucial tests is the insulation resistance test, which checks the quality of the transformer's insulation. This test is performed using a Megger, an instrument that applies a high voltage to the insulation material, measuring resistance to ensure it can effectively isolate the windings. Engineers with years of field experience often note that a healthy insulation resistance level indicates the transformer's preparedness for operation, reducing the likelihood of future insulation breakdowns.
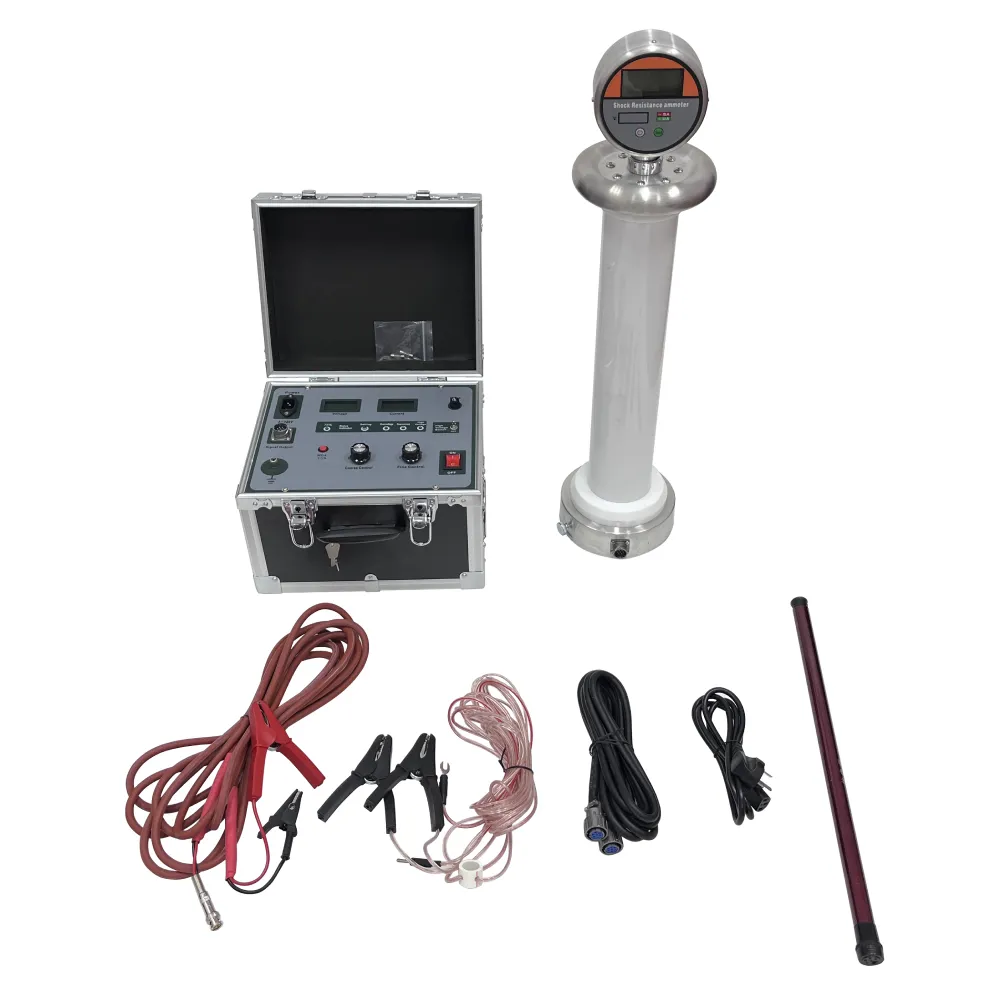
Another important test is the transformer turns ratio (TTR) test. This test verifies that the transformer has been wound correctly with the right ratios between the primary and secondary windings. Expertise in performing TTR tests is essential; even slight deviations from the expected ratio can signal winding issues that require addressing before full-scale operations.
The Dielectric Absorption Ratio (DAR) and Polarization Index (PI) tests are authoritative tests that further ascertain the insulation quality over extended periods. They are particularly important for high-voltage transformers where the risk of insulation failure poses significant operational and safety hazards. Conducting these tests requires in-depth knowledge and specialized equipment, reinforcing the importance of professional expertise in the evaluation process.
The oil quality test is another critical pre-commissioning assessment. Transformer oil is not just a cooling agent but also an insulator. Testing this oil helps in determining moisture content, acidity, and the presence of dielectric contaminants. Field experts often recommend oil tests as part of a systematic maintenance strategy, emphasizing their authoritative role in predictive maintenance models.
pre commissioning test of transformer pdf
Winding resistance measurement is also pivotal. It provides assurance that current will evenly distribute through the windings, minimizing losses and heat production. This test highlights issues such as poor conductor connections or contact problems in tap changers, which are often resolved through skilled interventions by experienced technicians before the transformer is energized.
Visual inspections, while seemingly basic, play a significant role as well. They offer insights into mechanical damage, ensuring that no apparent blockages or debris could impair performance. These inspections, when combined with comprehensive testing, greatly enhance the overall trustworthiness of the transformer when it is finally brought online.
Each of these tests requires a meticulous approach and should be documented meticulously, following established international standards such as IEC or IEEE. Such thorough documentation not only ensures compliance but also becomes a valuable resource for future reference, maintenance, and troubleshooting activities.
To sum up,
pre-commissioning tests of transformers are indispensable for securing operational longevity and reliability. By channeling a blend of experience from seasoned professionals, leveraging high-level expertise, adhering to authoritative standards, and fostering trust through rigorous testing protocols, these practices ensure transformers operate proficiently and securely within their designed parameters.
Engaging with these processes not only enhances the lifespan and reliability of transformers but also contributes to broader system efficiency and safety. Organizations that prioritize these protocols demonstrate a commitment to excellence, operational efficiency, and stakeholder trust, setting a benchmark for industry best practices.