The winding turns tester is an essential tool for evaluating the quality of wire windings in electric motors, transformers, and other inductive devices where precision and reliability are paramount. In the realm of power electronics, ensuring the accuracy of windings directly correlates with the efficiency and lifespan of the device. Delving into the intricacies of a winding turns tester, we explore its significance, operational principles, and best practices for achieving top-notch results.
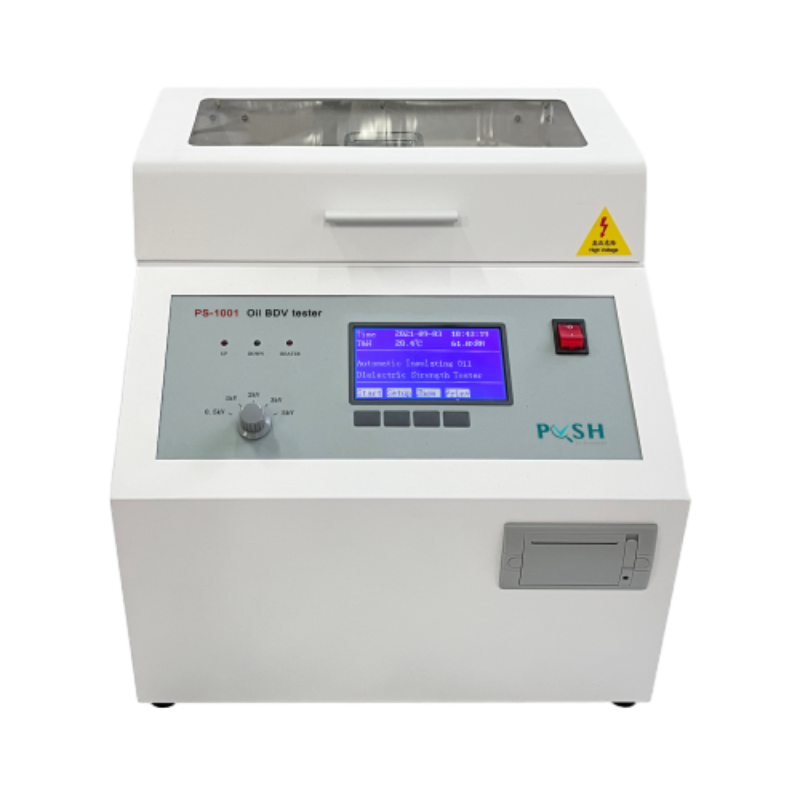
Precision in Winding Counts
The winding turns tester stands as the quintessential instrument for ensuring that coils are wound accurately.
Incorrect winding turns can lead to inefficiencies, overheating, and premature device failure. This device measures the number of turns in a coil with high precision. Its application is crucial in industries relying on transformers or coils where even a slight deviation in turns can lead to significant financial losses.
Advanced Technology Integration
Modern winding turns testers employ advanced microcontroller-based technology. This allows for faster and more reliable measurements. Embedded systems ensure minimal errors in counting, and some models even feature digital displays and automated report generation. By integrating cutting-edge technology, these devices meet and often exceed industry standards for testing accuracy, thus enhancing their credibility and trustworthiness among engineers and technicians.

User Experience and Practicality
From an operational perspective, user-friendliness is a critical component of any winding turns tester. Devices on the market today are often equipped with intuitive interfaces that allow for easy operation, even for those with minimal technical expertise. The user experience is further enhanced by features such as adjustable testing speeds, customizable settings, and portability. A tester that provides consistent, repeatable results without cumbersome setup is highly valued in any laboratory or manufacturing floor setting.
Calibration and Maintenance
A key part of leveraging the full potential of a winding turns tester is regular calibration. Proper calibration ensures the accuracy and reliability of measurements, which are essential for maintaining the quality of the end product. Many manufacturers recommend annual calibration as part of standard maintenance. Moreover, regular software updates can enhance the tester’s functionality, adding new features or improving existing ones.
Expertise and Training
For professionals using a winding turns tester, developing expertise is facilitated by comprehensive training. Many manufacturers offer dedicated training programs or detailed manuals that cover everything from setup to advanced troubleshooting. Training ensures that users not only understand how to operate the device but also how to interpret its results effectively. Advanced training modules might also cover aspects of data analysis and how to apply findings to improve production quality.
winding turns tester
Authoritative Testing Standards
The credibility of winding turns testers is underscored by adherence to international testing standards. Devices that comply with standards such as IEEE, ANSI, or IEC are typically regarded as more trustworthy. These standards serve as a benchmark for quality and reliability, offering users peace of mind that their testers provide precision measurements that align with global expectations.
Adapting to Diverse Applications
Winding turns testers are incorporated across a broad spectrum of industries, from automotive to aerospace, showcasing their versatility. They are specifically designed to handle various coils and transformers, no matter the application size or specifications. Such flexibility makes them an indispensable tool for companies looking to standardize their testing processes across different product lines.
Fostering Innovation
Inventors and product developers rely on winding turns testers to foster innovation in electrical design. By ensuring that prototypes and finished products meet stringent quality requirements, these devices enable the exploration of more efficient and compact winding techniques. This empowers engineers to push the boundaries of what’s possible in electrical design, leading to more innovative solutions.
Building Trust with Clients
For service providers that conduct testing on behalf of clients, a winding turns tester can be a crucial factor in building trust. Clients need assurance that their products are tested with accuracy and precision. Therefore, providers often emphasize their use of the latest, most reliable equipment to demonstrate their commitment to delivering high-quality testing services.
In conclusion, the winding turns tester is more than just a piece of equipment; it is a pivotal asset in ensuring product reliability and efficiency. From enhancing precision in manufacturing to bolstering innovation, winding turns testers form the backbone of quality assurance in electrical engineering. By selecting a tester that meets high standards of accuracy, user-friendliness, and versatility, companies can significantly enhance their reputation and trustworthiness within the industry.