Ensuring the seamless operation of transformers, induction motors, and alternators begins with rigorous testing protocols prior to their commissioning. Such protocols not only enhance the reliability of these machines but also extend their life span, proving crucial in industrial applications where downtime can be costly. The focus of these tests underscores a meticulous process crafted by experts in electrical engineering, prioritizing safety, performance, and efficiency from the very outset.
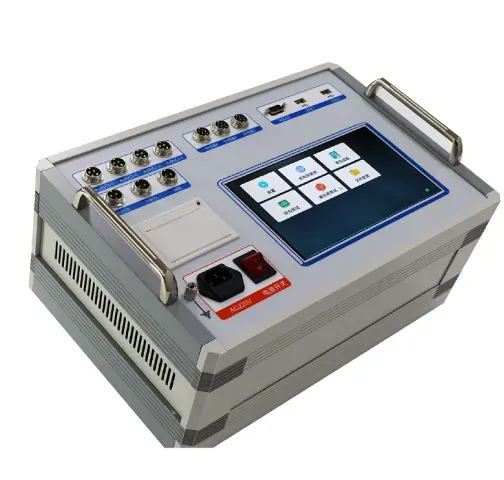
Transformers, the critical components in electrical distribution systems, require a series of precise tests before being brought online. These tests evaluate the transformer's ability to handle various loads, detect insulation weaknesses, and ensure no underlying mechanical issues could later result in failure. High-voltage testing, including withstand and impulse tests, are crucial for assessing insulation integrity. Additional assessments, such as turns ratio testing, loss measurement, and oil analysis, are fundamental in identifying inefficiencies and potential risks. These procedures ascertain the transformer's capability to perform under expected service conditions while adhering to industry standards.
Induction motors, widely used across industries due to their robustness and efficiency, similarly undergo extensive testing pre-commissioning. The testing begins with insulation resistance tests to ensure the motor's windings are not compromised. Phase balance and impedance tests follow, indicating whether electrical imbalances could lead to operational inefficiencies or premature wear. Load testing is essential, revealing how the motor performs under various operational stresses. This data, interpreted by skilled professionals, provides insights critical for optimizing the motor's operating settings for peak performance, thereby safeguarding against unforeseen breakdowns.

Alternators, pivotal in power generation, are subjected to stringent testing regimes before deployment. These tests validate the alternator's ability to convert mechanical energy into electrical energy efficiently and consistently. The verification process includes insulation resistance, resistance measurement, and performance testing under simulated load conditions. Voltage regulation and frequency response are evaluated to ensure output stability essential for sensitive electronic equipment. Additionally, the alternator's cooling systems are assessed to prevent overheating, a common failure mode in real-world operating environments. By confirming that alternators meet regulatory guidelines and performance standards, operators can trust their reliability and effectiveness.
tests before commissioning of transformer induction motor and alternator
Employing these rigorous test protocols before commissioning reinforces an organization's commitment to quality and operational excellence. This assurance extends beyond just meeting compliance and regulatory requirements, delving into the realm of optimizing performance, maximizing efficiency, and ensuring safety. It signals a proactive approach to maintenance that can significantly mitigate the risk of operational failures and unscheduled outages.
Harnessing extensive field experience and engineering expertise, each step within these testing procedures embodies the synthesis of theoretical knowledge and practical application. Experienced engineers leverage both cutting-edge diagnostic tools and time-tested methods to derive insights that inform strategic decisions in equipment deployment. This level of expertise instills confidence in stakeholders, reassuring them of the systems' integrity and readiness for service.
Through the lens of expertise and authority, deploying rigorous testing regimens underscores a business's commitment to best practices and quality assurance. It reflects a profound understanding of electrical systems' complexities, affirming the credibility of the professionals involved. By integrating these testing standards into regular maintenance schedules post-commissioning, organizations can further ensure the reliability and longevity of their critical infrastructure.
In conclusion,
the meticulous pre-commissioning tests on transformers, induction motors, and alternators are the bedrock of a resilient electrical infrastructure. Such diligence not only enhances operational efficiency and safety but also builds trust in the systems powering industries globally. By upholding these standards, companies not only protect their investments but also position themselves as leaders in a competitive landscape, where reliability and expertise serve as pivotal differentiators.