During the testing phase of a transformer, a meticulous and thorough approach is crucial to ensure its optimal performance and safety when deployed in real-world applications. Drawing from extensive experience in testing transformers, this article delves into the key aspects of transformer testing that contribute to robust operational assurance, covering both the technical expertise involved and the authoritative practices that build trustworthiness in the product.
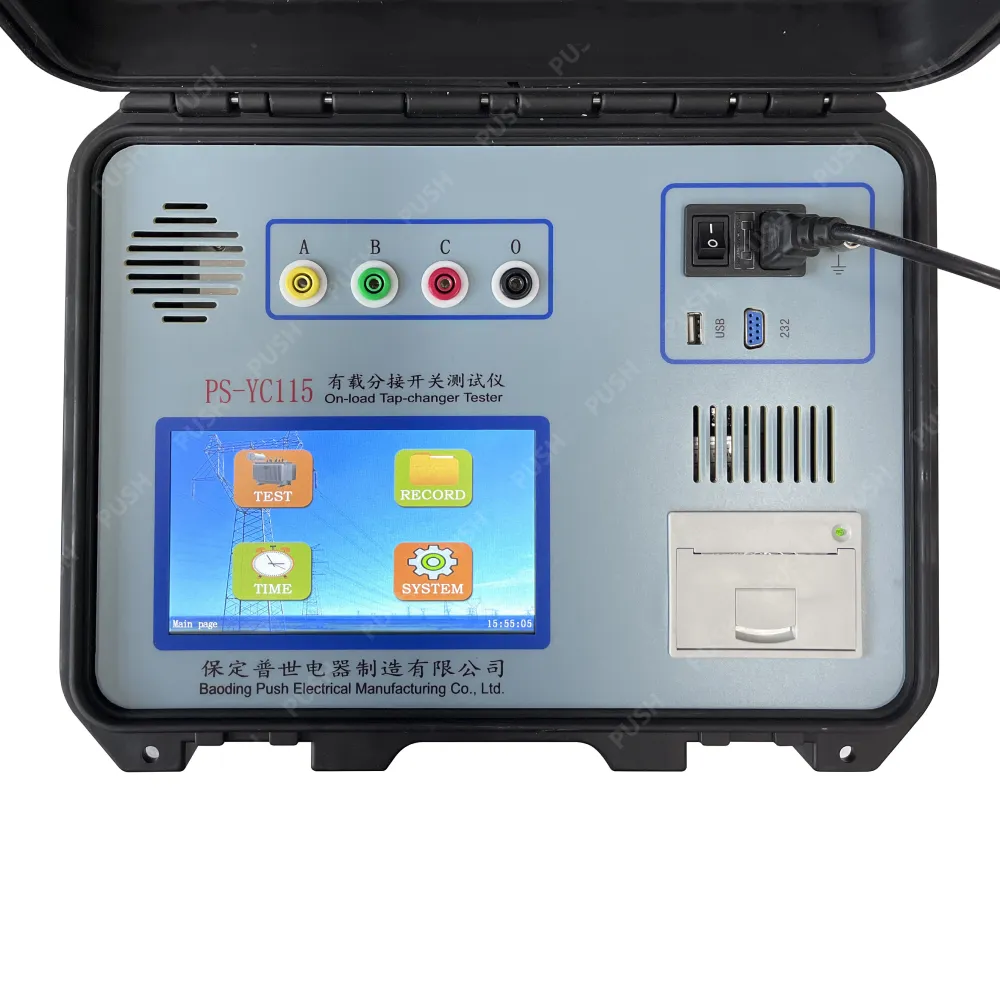
Transformers are the backbone of electrical systems, facilitating the effective transmission and distribution of electrical energy. Their performance is paramount to the reliability of energy networks, making the testing phase not only a technical necessity but a critical pillar in establishing product credibility. During testing, several parameters are scrutinized efficiency, voltage regulation, insulation integrity, and thermal performance, among others. Each of these parameters plays a significant role in the overall performance of the transformer.
First, efficiency measurements are essential. It's crucial to evaluate the transformer under different load conditions to determine how effectively it converts input power to output power. This involves analyzing both the no-load and full-load scenarios. Testing under these various conditions helps identify losses, such as copper losses due to electrical resistance and iron losses within the core material, which can be minimized through design improvements or material selection.
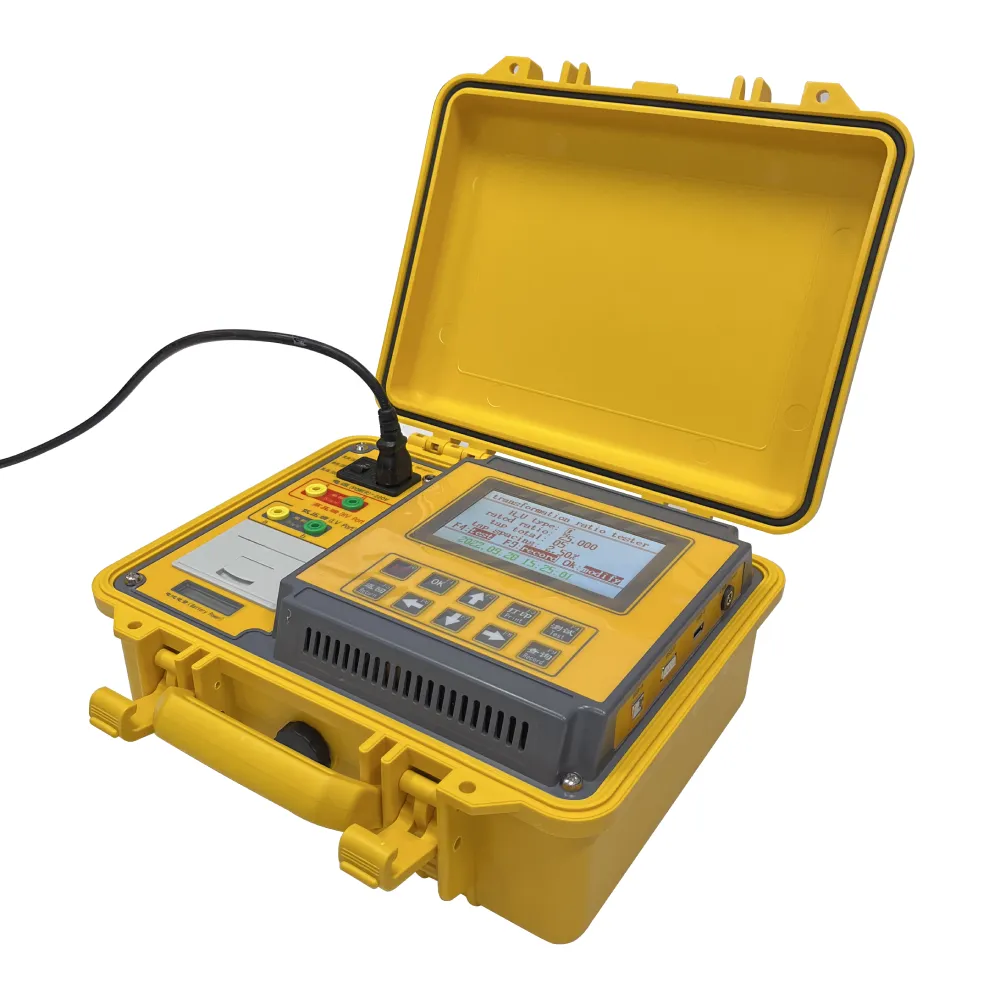
Voltage regulation testing is another critical aspect. It measures the transformer's ability to maintain a constant output voltage despite variations in load. This attribute is vital for ensuring the stability and reliability of the power supplied to end-users and can significantly impact user satisfaction and overall power quality. By testing a transformer's voltage regulation capabilities across different load conditions, engineers can assess its suitability for particular applications or need further enhancements.
Insulation is a foundational component in a transformer's safety and operational reliability. During testing, the insulation’s ability to withstand different electrical stresses without breakdown is evaluated. This typically involves high-voltage tests like the Lightning Impulse Test and Partial Discharge Test. These tests help detect imperfections within the insulation system, identifying potential points of failure before they manifest in service. The knowledge and experience of conducting such tests require a high level of expertise, showcasing the authoritative role of certified engineers in ensuring product quality.
during testing of a transformer
Thermal performance testing ensures the transformer can operate within safe temperature limits, preventing overheating and subsequent insulation damage. By simulating maximum operating conditions and monitoring the rise in temperature, engineers can validate the thermal design and confirm that the cooling systems are sufficient. This is crucial for transformers intended for high-demand applications where thermal stability and dissipation effectiveness are pivotal for continuous operation.
Furthermore, fault-tolerance testing is a significant part of the assessment process, examining how well a transformer handles sudden faults or abnormal operating conditions. Short-circuit tests, for example, help gauge the mechanical and thermal robustness of a transformer against unforeseen faults. This aspect of testing underscores the importance of a solid design and plays into the product's long-term reliability, which is a mark of trustworthiness in high-stakes applications.
Considerations for environmental impact are becoming increasingly important in transformer testing. This includes evaluating the transformer’s efficiency and emissions during operation, which align with sustainability goals and regulatory standards. By ensuring that transformers meet these environmental benchmarks, manufacturers not only demonstrate a commitment to responsible production but also align with broader ecological objectives, further enhancing the product's market reputation.
The testing phase concludes with a meticulous review and analysis of all data collected during the process. Through expert evaluation of these results, engineers can make informed decisions about the readiness of the transformer for production and deployment. This comprehensive understanding facilitates continuous improvement, as feedback is utilized to refine designs and enhance performance, embodying the principle of expertise-driven product development.
In conclusion, transformer testing is a rigorous procedure that demands a blend of experience, technical proficiency, and a commitment to quality assurance. By thoroughly evaluating all aspects of transformer performance, manufacturers can deliver products that not only meet but exceed industry standards, establishing their position as authoritative figures in the power systems domain. This dedication to excellence assures customers of the transformer's reliability and longevity, fostering trust through proven performance and meticulous attention to detail.