Resistance testing on transformers is a critical procedure that ensures the operational efficiency and safety of electrical systems. At its core, this testing identifies potential problems before they escalate, minimizing downtime and extending the lifespan of the equipment.
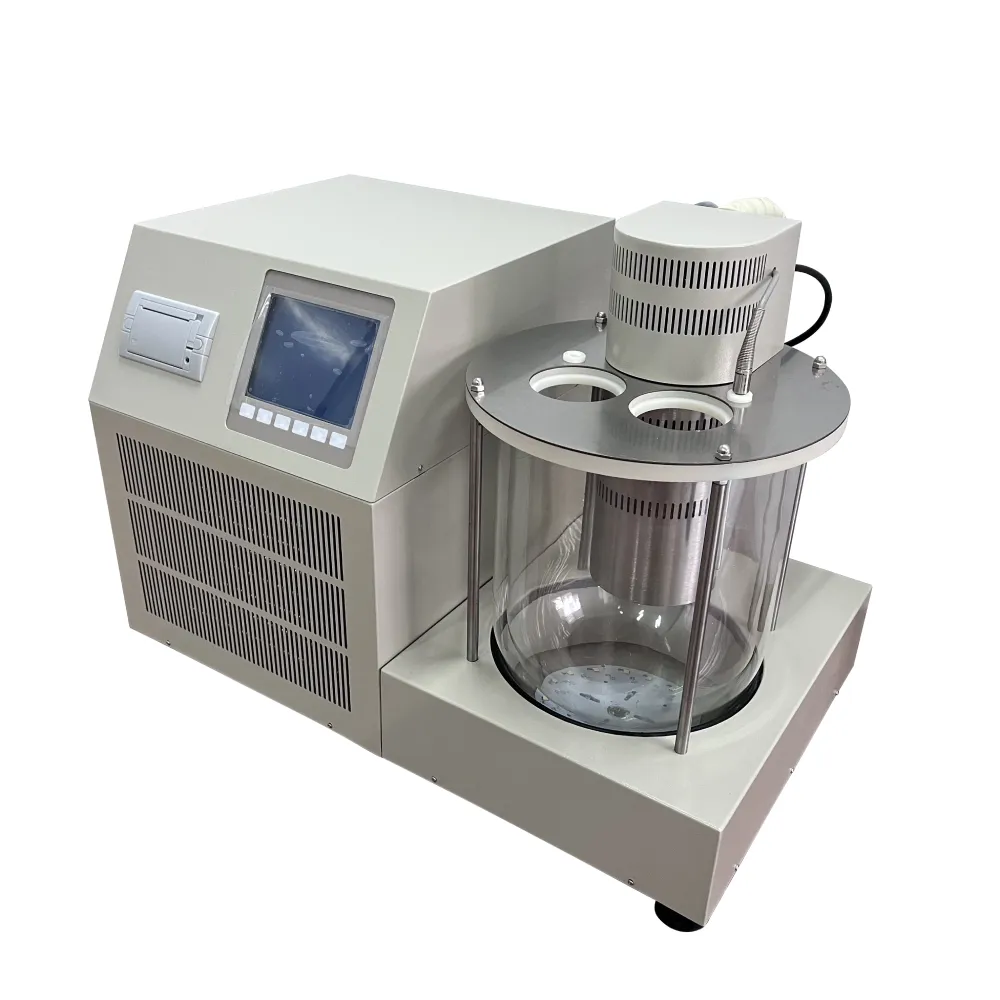
Transformers are integral in power distribution networks as they modulate voltage levels to ensure a seamless flow of electricity. However, like all electrical components, transformers are subject to wear and tear. Resistance testing—particularly winding resistance testing—plays a pivotal role in diagnosing and mitigating issues such as imbalances and internal faults.
The process of winding resistance testing involves assessing the ohmic resistance of the transformer's windings. This is crucial because discrepancies can indicate issues such as shorted turns, poor joints, or winding damage. Early detection of such problems through resistance testing can prevent catastrophic failures, thereby augmenting the reliability of power systems.

For an accurate resistance test, precision instrumentation is required. Using an Ohmmeter or a Digital Low Resistance Ohmmeter (DLRO) is ideal due to their capacity to deliver precise measurements. Before instigating the test, technicians must ensure that the transformer is de-energized to prevent electrical hazards. It's also essential to account for temperature, as resistance values can fluctuate with varying temperatures—which necessitates the application of temperature correction factors to standardize readings.
In practice, resistance measurements are taken at different tap positions to ensure comprehensive assessment. Deviations in expected resistance values could signify issues and warrant further investigation. It's recommended that testing be performed under ambient conditions if possible and compared against the manufacturer's standard resistance values.
resistance test on transformer
Moreover, documentation is an indispensable component of resistance testing. Recording initial measurements provides a baseline. Over time, regular tests can highlight trends, enabling predictive maintenance and proactive problem-solving. This can be an invaluable asset for facilities management, enhancing the resilience of the power distribution infrastructure.
In addition to understanding the technical nuances, transformer resistance testing also necessitates specialized expertise and training. It is the responsibility of the testing team to follow international standards such as IEEE and IEC guidelines, ensuring it's executed correctly and safely. These guidelines provide structured methodologies for accurate testing, which inherently boosts trustworthiness in the test outcomes.
Furthermore, maintaining high standards of safety during testing is non-negotiable. Technicians need to employ the necessary safety gear and adhere strictly to established safety protocols. A misjudgment could lead to severe occupational hazards or equipment damage. Hence, comprehensive training programs and certifications for electrical professionals handling transformers are highly recommended, reinforcing both safety and expertise.
The practice of resistance testing is not only about accurate measurements and safety. It's about ensuring customers and businesses experience minimal disruptions by reducing unexpected power outages. This reliability factor significantly enhances the perceived authoritativeness and trustworthiness of the service providers involved.
In conclusion, resistance test on transformers is indispensable for predictive maintenance and operational excellence. By adhering to best practices, utilizing the correct equipment, and following international standards, businesses can ensure their power distribution systems are stable and efficient. Regular resistance testing secures the future of energy flow, safeguarding both infrastructure investments and end-user satisfaction.